The late machine incident has become a critical concern across various industries, affecting productivity, operational efficiency, and even safety in some cases. Whether it's manufacturing, healthcare, or transportation, delays in machine performance can lead to significant disruptions. In this article, we will explore the root causes of late machine incidents, their impacts, and strategies to mitigate them effectively.
As technology continues to evolve, reliance on machines has increased exponentially. However, with this reliance comes the responsibility to ensure that these machines function optimally at all times. A late machine incident refers to any situation where a machine fails to operate as scheduled, leading to delays in processes or operations. Understanding this phenomenon is crucial for organizations aiming to minimize downtime and maximize productivity.
This article aims to provide a comprehensive overview of late machine incidents, offering actionable insights and solutions. By the end of this article, you will have a clear understanding of the factors contributing to these incidents and how to address them effectively.
Read also:Andrew Burkle The Legacy And Impact Of His Passing
Table of Contents
- What is a Late Machine Incident?
- Common Causes of Late Machine Incidents
- Impact of Late Machine Incidents on Business
- Preventive Measures to Avoid Late Machine Incidents
- Maintenance Strategies for Machines
- Technological Solutions for Late Machine Incidents
- Cost Analysis of Late Machine Incidents
- Case Studies: Real-Life Examples of Late Machine Incidents
- Best Practices for Managing Machine Performance
- Conclusion: Taking Action Against Late Machine Incidents
What is a Late Machine Incident?
A late machine incident refers to any occurrence where a machine fails to perform as expected, resulting in delays or disruptions in operations. These incidents can happen due to various reasons, such as mechanical failures, software glitches, or human error. The impact of these incidents can vary from minor inconveniences to significant financial losses, depending on the scale and nature of the operation.
In the context of manufacturing, a late machine incident could mean a production line coming to a halt, leading to missed deadlines and dissatisfied customers. Similarly, in healthcare, a delay in medical equipment functioning can jeopardize patient safety and care.
Understanding the definition and scope of late machine incidents is the first step toward addressing them effectively. This section provides an overview of what constitutes a late machine incident and its relevance in today's industrial landscape.
Common Causes of Late Machine Incidents
1. Mechanical Failures
Mechanical failures are one of the primary reasons behind late machine incidents. Components such as motors, gears, and belts can wear out over time, leading to unexpected breakdowns. Regular inspections and timely replacements can help mitigate these risks.
2. Software Glitches
In the era of Industry 4.0, machines are increasingly reliant on software for their operations. Software bugs or malfunctions can disrupt machine performance, causing delays. Implementing robust software testing and maintenance protocols is essential to prevent such issues.
3. Human Error
Human error remains a significant factor in late machine incidents. Mistakes during machine setup, operation, or maintenance can lead to inefficiencies and delays. Providing adequate training and implementing standard operating procedures (SOPs) can reduce the likelihood of human-induced errors.
Read also:Lexi2legit Erome A Comprehensive Guide To Understanding The Phenomenon
- Inadequate training of machine operators
- Failure to follow maintenance schedules
- Improper handling of equipment
Impact of Late Machine Incidents on Business
The consequences of late machine incidents can be far-reaching, affecting both the bottom line and the reputation of a business. Financial losses due to downtime, increased maintenance costs, and potential legal liabilities can strain an organization's resources. Additionally, customer dissatisfaction and loss of trust can harm long-term relationships.
Studies show that unplanned downtime can cost businesses an average of $260,000 per hour, depending on the industry. In sectors like automotive manufacturing, the costs can escalate even further, with some estimates reaching millions of dollars per hour of downtime.
Moreover, the intangible impacts, such as damage to brand reputation, can have lasting effects. Customers expect reliability and consistency, and any deviation from these expectations can lead to a decline in market share and competitive advantage.
Preventive Measures to Avoid Late Machine Incidents
1. Predictive Maintenance
Predictive maintenance involves using data analytics and sensors to monitor machine performance and predict potential failures before they occur. This proactive approach can significantly reduce the likelihood of late machine incidents.
2. Regular Inspections
Scheduling regular inspections and maintenance checks is crucial in identifying and addressing issues before they escalate. This practice ensures that machines operate at optimal levels and minimizes the risk of unexpected breakdowns.
3. Training and Development
Investing in employee training programs can enhance their skills and knowledge, reducing the chances of human error. Well-trained staff are better equipped to handle machines efficiently and troubleshoot issues promptly.
By implementing these preventive measures, organizations can create a more reliable and efficient operational environment.
Maintenance Strategies for Machines
Effective maintenance strategies are essential for preventing late machine incidents. These strategies involve a combination of preventive, predictive, and corrective maintenance approaches tailored to the specific needs of each machine.
- Preventive maintenance: Scheduled servicing and part replacements
- Predictive maintenance: Monitoring machine health using sensors and analytics
- Corrective maintenance: Addressing issues as they arise
Adopting a balanced approach that incorporates all three strategies can optimize machine performance and reduce downtime.
Technological Solutions for Late Machine Incidents
1. Internet of Things (IoT)
The Internet of Things (IoT) enables machines to communicate with each other and share data in real-time. This connectivity allows for continuous monitoring and early detection of potential issues, reducing the occurrence of late machine incidents.
2. Artificial Intelligence (AI)
Artificial Intelligence (AI) can analyze vast amounts of data to identify patterns and predict machine failures. AI-driven systems can provide actionable insights and recommendations to prevent incidents before they happen.
3. Cloud Computing
Cloud computing offers scalable storage and processing capabilities, enabling organizations to store and analyze machine data efficiently. This technology facilitates remote monitoring and management of machines, enhancing operational efficiency.
Cost Analysis of Late Machine Incidents
Understanding the financial implications of late machine incidents is crucial for businesses. The costs associated with these incidents can be categorized into direct and indirect costs. Direct costs include repair expenses, replacement parts, and labor. Indirect costs encompass lost productivity, customer dissatisfaction, and potential legal liabilities.
A study by McKinsey & Company reveals that companies in the manufacturing sector can lose up to 20% of their productive capacity due to unplanned downtime. This loss translates into millions of dollars annually, emphasizing the need for effective incident management strategies.
By conducting a thorough cost analysis, organizations can allocate resources more efficiently and prioritize investments in preventive measures and technological solutions.
Case Studies: Real-Life Examples of Late Machine Incidents
Case Study 1: Automotive Manufacturing Plant
A major automotive manufacturing plant experienced a late machine incident when a critical assembly line machine failed unexpectedly. The incident resulted in a two-day shutdown, costing the company approximately $5 million in lost production and additional repair expenses. Post-incident analysis revealed that inadequate maintenance schedules and lack of predictive analytics were the primary causes.
Case Study 2: Hospital Imaging Department
A hospital faced a late machine incident when its MRI machine malfunctioned during peak hours. The delay in diagnostic procedures affected patient care and caused a backlog of appointments. The hospital implemented a predictive maintenance system afterward, reducing the likelihood of similar incidents in the future.
These case studies highlight the importance of proactive measures in preventing late machine incidents and their potential consequences.
Best Practices for Managing Machine Performance
Adopting best practices is essential for ensuring optimal machine performance and minimizing the risk of late machine incidents. Some of these practices include:
- Implementing a comprehensive maintenance schedule
- Utilizing advanced analytics and IoT technologies
- Providing ongoing training and development opportunities for employees
- Establishing clear communication channels for reporting issues
By following these best practices, organizations can create a culture of reliability and efficiency, ultimately leading to improved operational outcomes.
Conclusion: Taking Action Against Late Machine Incidents
In conclusion, late machine incidents pose significant challenges to businesses across various industries. Understanding their causes, impacts, and solutions is vital for organizations aiming to maintain operational excellence. By implementing preventive measures, adopting technological solutions, and following best practices, companies can effectively mitigate the risks associated with these incidents.
We invite you to take action by reviewing your current maintenance strategies and exploring new technologies that can enhance machine performance. Share your thoughts and experiences in the comments section below, and consider exploring other articles on our site for more insights into industrial efficiency and innovation.
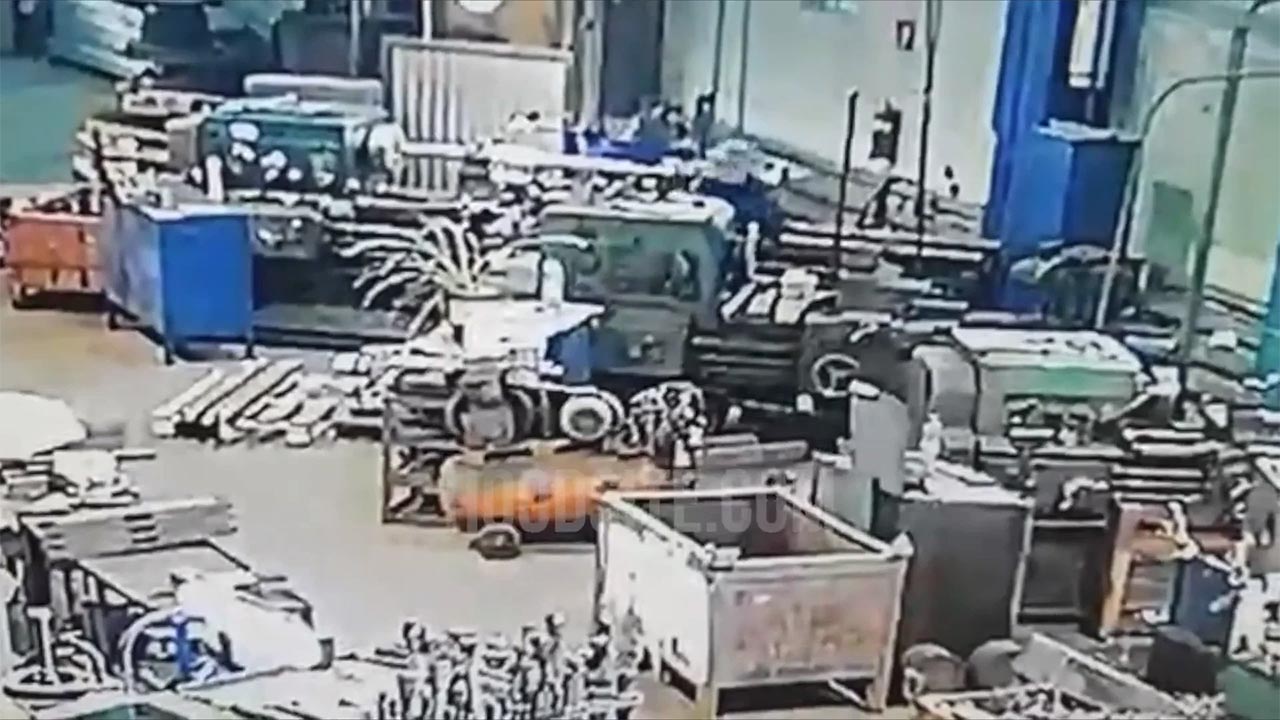
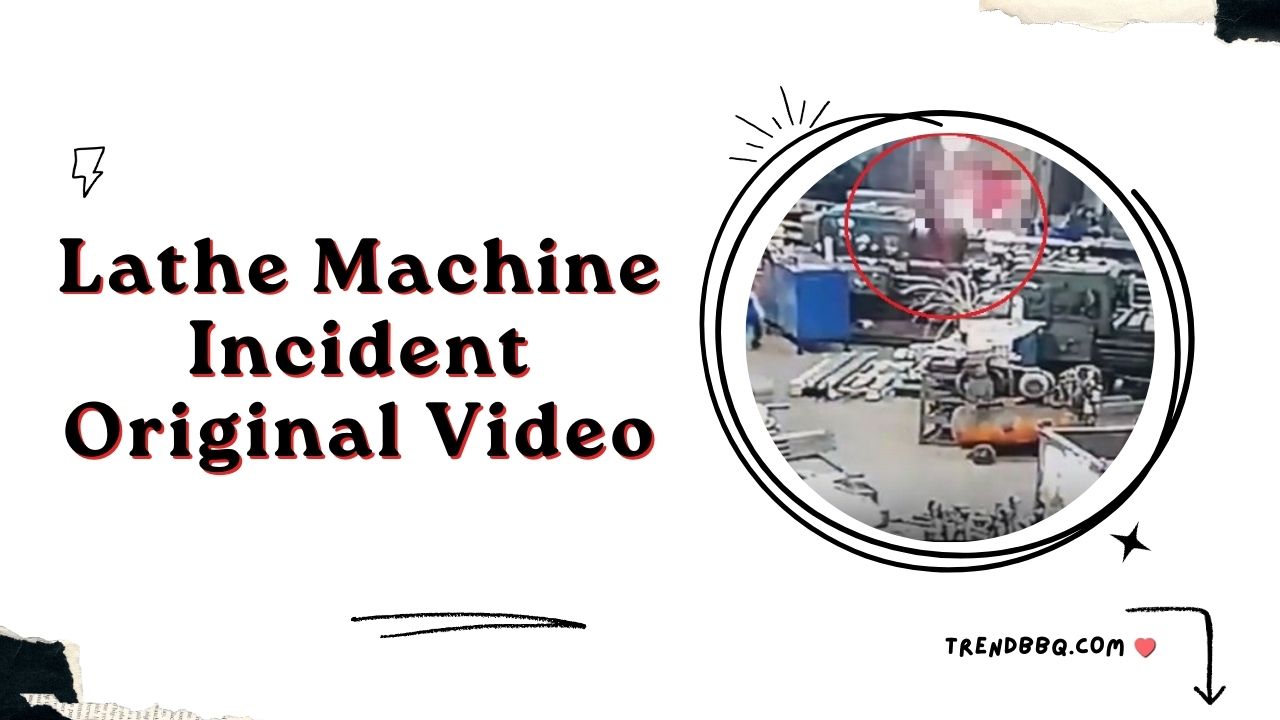