Lathe machine accidents are a serious concern in the manufacturing and engineering industries. These machines, although essential for shaping and cutting materials, can pose significant risks to operators if not handled properly. Understanding the causes of lathe machine accidents is crucial to ensuring workplace safety and preventing potential injuries. This article will delve into the common factors contributing to these accidents, explore preventive measures, and highlight the importance of adhering to safety protocols.
As industrial operations continue to grow, so does the reliance on machinery like lathes. While they are indispensable for precision work, they also come with inherent dangers. Operators must be aware of these risks and take necessary precautions to minimize accidents. By understanding the root causes of lathe machine accidents, we can better equip ourselves with knowledge to foster a safer working environment.
This comprehensive guide aims to provide detailed insights into lathe machine accidents, focusing on causes, prevention strategies, and safety measures. Whether you're an operator, supervisor, or safety professional, this article offers valuable information to enhance your understanding and contribute to accident-free workplaces.
Read also:Silent Omnibus Manga A Comprehensive Dive Into The World Of Silent Manga
Table of Contents
- Introduction to Lathe Machines
- Common Causes of Lathe Machine Accidents
- Statistics on Lathe Machine Accidents
- Safety Protocols for Lathe Operations
- Preventive Measures to Reduce Accidents
- Personal Protective Equipment (PPE)
- Training and Certification for Operators
- Importance of Maintenance and Inspection
- Case Studies of Lathe Machine Accidents
- Conclusion and Final Thoughts
Introduction to Lathe Machines
Lathe machines are versatile tools used for shaping materials such as metal, wood, and plastic by rotating them on an axis. They are widely used in industries ranging from automotive to aerospace. The fundamental operation of a lathe involves clamping the material to be worked on and rotating it while a cutting tool shapes the material to the desired dimensions.
Despite their efficiency, lathe machines can be hazardous if mishandled. Operators must understand the mechanics of the machine and the safety precautions required to operate it effectively. This section will explore the basic components of a lathe machine and its role in modern manufacturing.
Key Components of a Lathe Machine
- Headstock: Holds the spindle and drives the rotation of the material.
- Tailstock: Provides support to the other end of the material being worked on.
- Tool Post: Mounts the cutting tool that shapes the material.
- Bed: The base that supports all the components of the machine.
Common Causes of Lathe Machine Accidents
Lathe machine accidents can occur due to a variety of factors, ranging from human error to mechanical failure. Identifying these causes is the first step in preventing accidents. Below are some common causes:
- Inadequate training of operators.
- Failure to use personal protective equipment (PPE).
- Improper maintenance of the machine.
- Loose clothing or jewelry getting caught in the machine.
Human Error
Human error remains one of the leading causes of lathe machine accidents. Operators who are not properly trained or are distracted while operating the machine are at higher risk of accidents. Ensuring that all operators undergo comprehensive training programs is essential to minimize human error.
Statistics on Lathe Machine Accidents
Data from industrial safety reports indicate that lathe machine accidents account for a significant percentage of workplace injuries. According to the Occupational Safety and Health Administration (OSHA), approximately 8% of all machine-related accidents involve lathes. These accidents often result in severe injuries, including amputations and fractures.
A study conducted by the National Institute for Occupational Safety and Health (NIOSH) revealed that inadequate safety training and lack of proper maintenance were the primary contributing factors to these accidents.
Read also:Does Parker Schnabel Have A Wife Unveiling The Personal Life Of The Gold Rush Star
Safety Protocols for Lathe Operations
Establishing and enforcing safety protocols is critical to preventing lathe machine accidents. These protocols should cover all aspects of machine operation, from setup to shutdown. Below are some key safety protocols:
- Ensure all guards and safety devices are in place before operation.
- Conduct regular inspections and maintenance checks.
- Prohibit the use of loose clothing or jewelry while operating the machine.
Emergency Stop Procedures
Every lathe machine should be equipped with an emergency stop button. Operators must be trained on how and when to use this feature in case of an accident or malfunction. Quick access to the emergency stop can prevent serious injuries.
Preventive Measures to Reduce Accidents
Preventive measures are proactive steps taken to reduce the likelihood of accidents. These measures include:
- Regular safety audits and risk assessments.
- Providing ongoing training and education for operators.
- Implementing a robust maintenance schedule.
Technology and Automation
Advancements in technology have led to the development of automated lathe machines that reduce the need for direct operator intervention. These machines incorporate safety features such as sensors and automated shut-off mechanisms, further enhancing workplace safety.
Personal Protective Equipment (PPE)
PPE is essential for protecting operators from potential hazards. The following items are recommended:
- Safety goggles to protect eyes from debris.
- Gloves to prevent hand injuries.
- Steel-toed boots to protect feet from falling objects.
Importance of PPE Compliance
Compliance with PPE regulations is mandatory in most industrial settings. Employers must ensure that operators have access to the necessary equipment and are trained on its proper use. Regular inspections should be conducted to verify compliance.
Training and Certification for Operators
Training and certification programs play a vital role in reducing lathe machine accidents. Operators should undergo comprehensive training that covers both theoretical and practical aspects of machine operation. Certification programs provided by recognized institutions can enhance operator competence and confidence.
Continuous Learning
As technology evolves, so should the skills of operators. Continuous learning programs can help operators stay updated with the latest safety practices and machine advancements.
Importance of Maintenance and Inspection
Regular maintenance and inspection of lathe machines are crucial for preventing accidents. A well-maintained machine is less likely to malfunction, reducing the risk of accidents. Inspections should be conducted by qualified technicians who can identify potential issues before they become serious problems.
Scheduled Maintenance
Scheduling regular maintenance checks ensures that all components of the lathe machine are functioning correctly. This proactive approach can extend the lifespan of the machine and enhance its performance.
Case Studies of Lathe Machine Accidents
Examining real-life case studies can provide valuable insights into the causes and consequences of lathe machine accidents. Below are two examples:
Case Study 1: Improper Training
In a manufacturing plant, an inexperienced operator suffered a severe hand injury after failing to use the correct tooling technique. The accident was attributed to inadequate training, highlighting the importance of comprehensive operator education.
Case Study 2: Mechanical Failure
A lathe machine malfunctioned during operation, resulting in a piece of metal flying off and injuring an operator. Further investigation revealed that the machine had not been inspected for several months, emphasizing the need for regular maintenance checks.
Conclusion and Final Thoughts
Lathe machine accidents are preventable with the right combination of training, maintenance, and safety protocols. By understanding the causes of these accidents and implementing preventive measures, we can significantly reduce the risk of injuries in the workplace.
We encourage readers to share their thoughts and experiences in the comments section below. Additionally, feel free to explore other articles on our site for more insights into industrial safety and best practices. Together, we can create safer working environments for everyone.
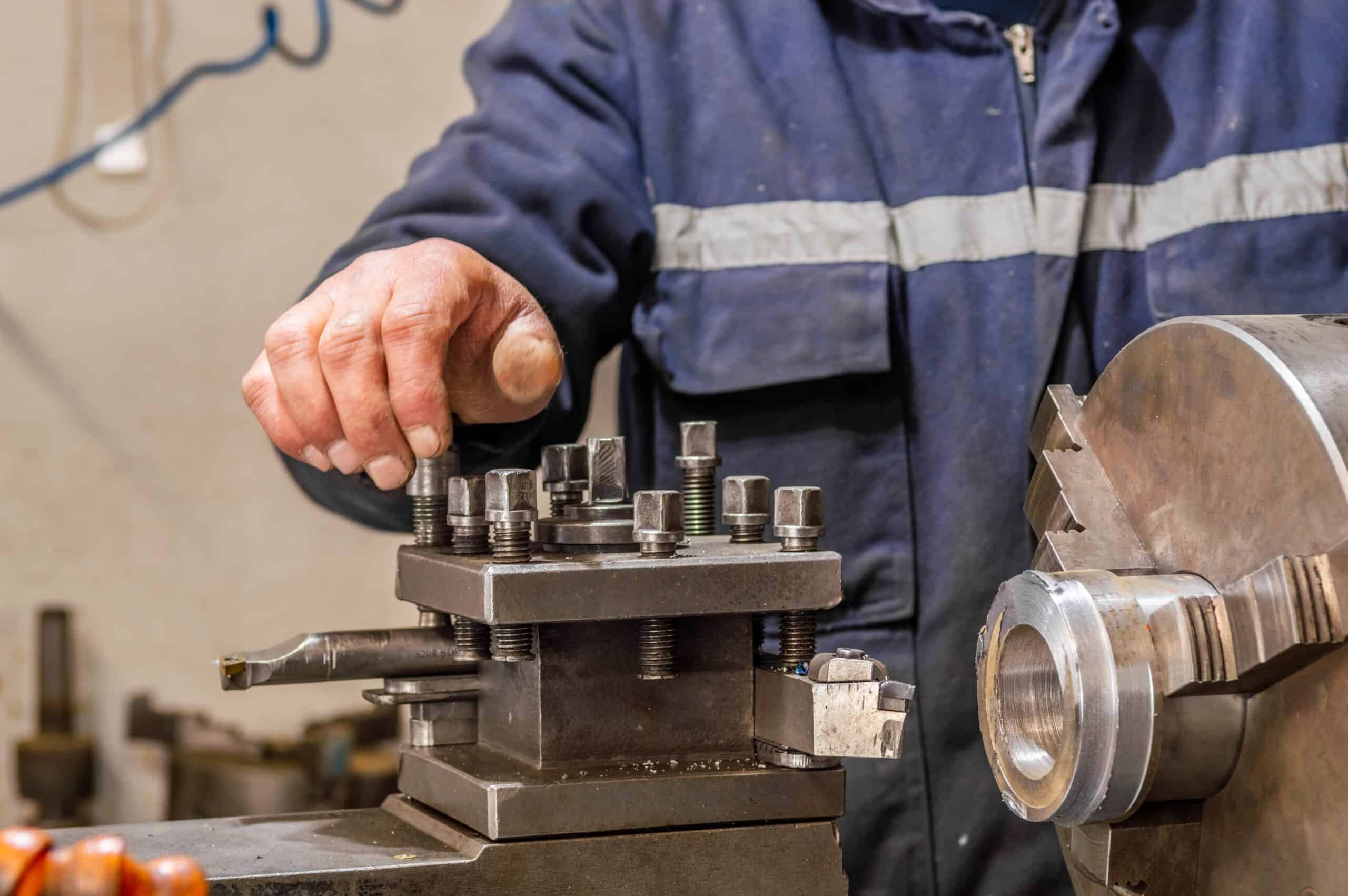
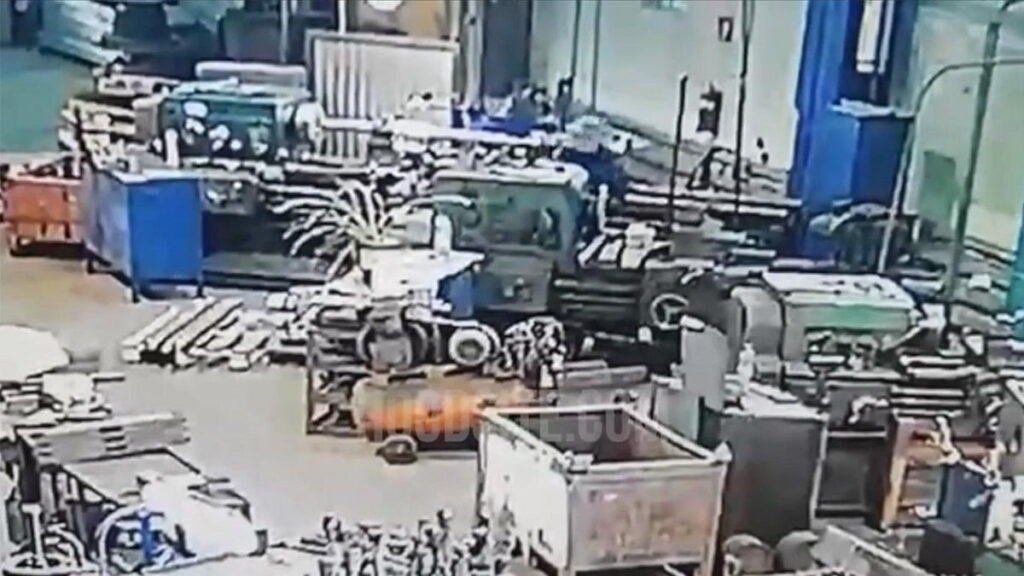