Lathe accidents are a serious concern in the manufacturing industry, often resulting in severe injuries or even fatalities. According to the Occupational Safety and Health Administration (OSHA), machine-related accidents account for a significant portion of workplace injuries. Lathes, in particular, are among the most commonly used machines in workshops and factories, but they also pose significant risks if not handled properly.
As industries continue to rely heavily on machinery for precision work, understanding the causes of lathe accidents and implementing preventive measures becomes crucial. This article aims to provide a comprehensive overview of lathe accidents, their causes, prevention strategies, and safety protocols that can significantly reduce the risk of injury.
Whether you're a seasoned machinist, a safety officer, or someone new to the field, this guide will equip you with the knowledge and tools necessary to ensure a safer working environment. Let's dive in and explore how we can minimize the risks associated with lathe operations.
Read also:Tyler Nixon The Rising Star In The World Of Entertainment
Table of Contents
- Introduction to Lathe Accidents
- Common Causes of Lathe Accidents
- Prevention Strategies
- Safety Training
- Types of Lathe Injuries
- Statistics on Lathe Accidents
- Role of OSHA in Preventing Lathe Accidents
- Case Studies
- Best Practices for Safe Lathe Operation
- Conclusion and Call to Action
Introduction to Lathe Accidents
A lathe is a versatile machine tool used for shaping metal, wood, or other materials by rotating them against a cutting tool. Despite its utility, lathes can be dangerous if not operated with care. Lathe accidents can occur due to a variety of reasons, ranging from operator error to machine malfunction.
Understanding the basics of lathe operations is essential for preventing accidents. Proper training, adherence to safety protocols, and regular maintenance of equipment are key factors in reducing the risk of injury. In this section, we will explore the fundamental aspects of lathe accidents and why they happen.
Common Causes of Lathe Accidents
Lathe accidents often stem from a combination of human error and mechanical issues. Below are some of the most common causes:
- Improper training or lack of experience
- Failure to use personal protective equipment (PPE)
- Loose clothing or jewelry getting caught in the machine
- Inadequate machine maintenance
- Using the wrong tools or improper setup
Each of these factors can contribute to serious accidents, making it crucial for operators to be aware of potential hazards and take necessary precautions.
Prevention Strategies
Preventing lathe accidents requires a multi-faceted approach that includes proper training, equipment maintenance, and adherence to safety protocols. Below are some key prevention strategies:
Personal Protective Equipment
Using the right PPE is one of the most effective ways to prevent lathe accidents. Operators should always wear:
Read also:Andrew Huberman Girlfriend Exploring The Life And Relationship Behind The Neuroscience Guru
- Safety goggles to protect against flying debris
- Gloves to prevent cuts and abrasions
- Steel-toed boots to protect feet from falling objects
- Hearing protection to reduce noise exposure
Ensuring that all operators are equipped with the necessary PPE can significantly reduce the risk of injury.
Machine Maintenance
Regular maintenance of lathe machines is essential for preventing accidents. This includes:
- Inspecting the machine for wear and tear
- Ensuring all guards and safety features are functioning properly
- Replacing worn-out parts promptly
By keeping machines in optimal condition, operators can minimize the risk of malfunctions that could lead to accidents.
Safety Training
Proper training is vital for ensuring that operators understand the risks associated with lathe operations and how to mitigate them. Training programs should cover:
- Basic machine operation
- Safety protocols and procedures
- Emergency response plans
Regular refresher courses and hands-on practice can help reinforce the importance of safety and ensure that operators remain vigilant.
Types of Lathe Injuries
Lathe accidents can result in a wide range of injuries, some of which can be life-threatening. Common types of lathe injuries include:
- Cuts and lacerations from sharp tools
- Amputations caused by entanglement
- Eye injuries from flying debris
- Fractures and broken bones from falls or impacts
Understanding the potential consequences of lathe accidents highlights the importance of taking preventive measures to protect operators.
Statistics on Lathe Accidents
Data from OSHA and other safety organizations provide valuable insights into the prevalence and severity of lathe accidents. According to a report by OSHA, machine-related accidents account for approximately 8% of all workplace injuries in the manufacturing sector. Of these, lathes are among the most frequently involved machines.
Furthermore, studies show that a significant percentage of lathe accidents occur due to operator error, underscoring the need for comprehensive training and adherence to safety protocols.
Role of OSHA in Preventing Lathe Accidents
The Occupational Safety and Health Administration (OSHA) plays a critical role in regulating workplace safety standards. OSHA provides guidelines and regulations specifically designed to prevent lathe accidents, including:
- Requirements for machine guarding
- Mandates for safety training programs
- Standards for personal protective equipment
By enforcing these regulations, OSHA helps ensure that workplaces are safe and compliant with industry standards.
Case Studies
Examining real-world case studies can provide valuable lessons in preventing lathe accidents. For example, a recent incident at a manufacturing plant resulted in a severe hand injury when an operator failed to use the proper guarding equipment. This case highlights the importance of adhering to safety protocols and using the correct tools and equipment.
Another case involved a lathe malfunction that led to a catastrophic failure, emphasizing the need for regular maintenance and inspections.
Best Practices for Safe Lathe Operation
Implementing best practices is essential for ensuring safe lathe operation. Below are some key practices to consider:
Pre-Operation Checklist
Before starting a lathe operation, operators should complete a pre-operation checklist, which includes:
- Inspecting the machine for any visible defects
- Ensuring all safety guards are in place
- Checking that the workpiece is securely clamped
Completing this checklist can help identify potential issues before they become serious problems.
Post-Operation Procedures
After completing a lathe operation, operators should follow post-operation procedures, such as:
- Turning off the machine and allowing it to come to a complete stop
- Removing all tools and workpieces from the machine
- Conducting a final inspection to ensure everything is in order
These procedures help ensure that the machine is left in a safe and ready state for the next use.
Conclusion and Call to Action
Lathe accidents can have serious consequences, but they are preventable with the right strategies and practices in place. By understanding the causes of lathe accidents, implementing preventive measures, and adhering to safety protocols, operators can significantly reduce the risk of injury.
We encourage all readers to take an active role in promoting workplace safety. Share this article with colleagues and friends, and consider participating in safety training programs to enhance your knowledge and skills. Together, we can create a safer working environment for everyone.
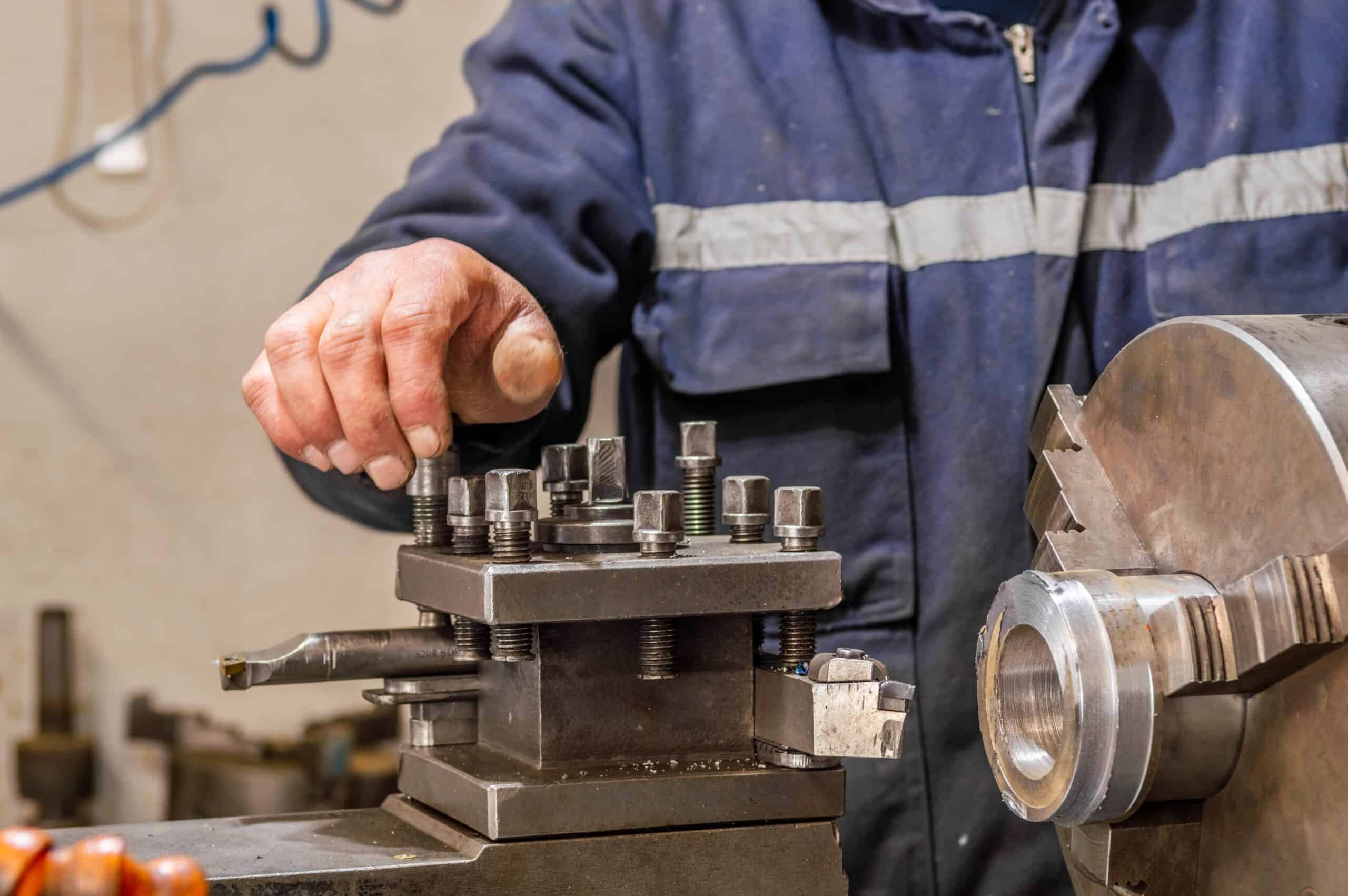
